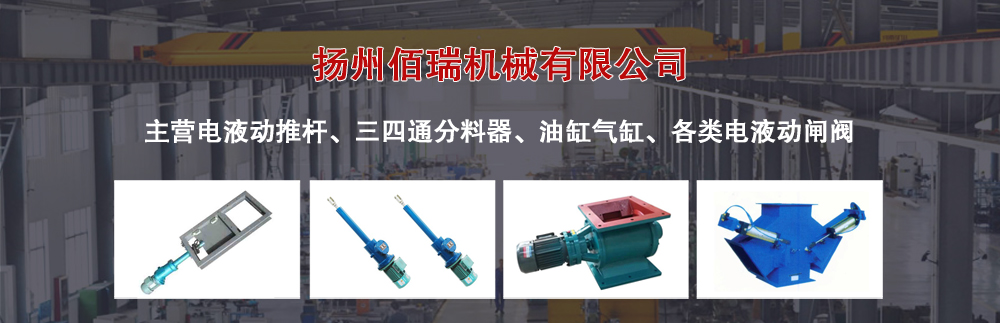
液压纠偏装置作为现代工程机械中的重要组成部分,其性能直接影响设备的精度与稳定性。如何优化液压纠偏装置的性能,成为许多工程机械制造企业关注的焦点。本文将从液压纠偏技术的原理、应用现状及其存在的问题入手,探讨优化液压纠偏装置性能的方法与策略。
液压纠偏装置的工作原理是利用液压系统的液压缸,通过液压油的压力传递,来纠正机械设备在工作过程中的偏差。液压系统的灵敏度、响应速度以及压力控制的精度,都是影响液压纠偏装置性能的关键因素。
目前,液压纠偏技术已经广泛应用于各种工程机械设备,如挖掘机、推土机、起重机等。随着市场竞争的加剧和用户对工程机械性能要求的不断提高,传统的液压纠偏装置在一些方面仍存在不足。例如,液压系统响应速度慢、精度不足、能耗高等问题,制约了设备的整体性能。
为了解决这些问题,优化液压纠偏装置性能的方法主要包括以下几个方面:
提升液压系统的响应速度:通过改进液压泵和液压缸的设计,采用高效能的液压油和更为先进的液压控制阀,提高液压系统的响应速度,使其能够更快速地纠正设备偏差。
提高液压系统的控制精度:利用先进的传感器技术和电子控制系统,实时监测设备的工作状态,并进行精准的液压压力调节,从而提升液压纠偏装置的控制精度。
降低液压系统的能耗:采用节能型液压元件和优化液压管路设计,减少液压油在传递过程中的能量损失,降低液压系统的能耗,提升设备的整体能效。
改进液压油的质量:使用高品质的液压油,保证液压系统在高负荷工作条件下的稳定性和耐久性,延长液压纠偏装置的使用寿命。
通过以上方法,液压纠偏装置的性能得到了显著提升,不仅提高了工程机械设备的工作精度和稳定性,还降低了设备的运行成本,提升了市场竞争力。
仅仅通过提升液压系统的硬件性能来优化液压纠偏装置是远远不够的。随着智能制造技术的迅猛发展,将信息技术与液压纠偏技术深度融合,成为未来液压纠偏装置性能优化的关键方向。
引入智能控制技术:在液压纠偏装置中引入智能控制系统,利用人工智能和机器学习算法,对设备的工作状态进行实时分析和预测,自动调整液压系统的参数,实现更加精准和高效的纠偏控制。例如,通过对历史数据的学习,智能控制系统能够预判设备的偏差趋势,提前进行纠偏操作,进一步提高设备的工作效率和精度。
建立故障诊断与预测系统:通过传感器和数据采集系统,实时监测液压纠偏装置的运行状态,并对数据进行分析,及时发现潜在的故障隐患。结合大数据分析和云计算技术,建立故障诊断与预测系统,提前采取维护措施,避免因设备故障导致的生产停滞和经济损失。
优化液压系统的动态性能:液压系统的动态性能对纠偏效果有着直接影响。通过仿真技术和实验测试,优化液压系统的动态响应特性,确保在各种工况下,液压纠偏装置都能保持稳定的工作状态。利用先进的控制算法,如PID控制、模糊控制等,进一步提高液压系统的动态性能和抗干扰能力。
加强液压纠偏装置的整体设计:优化液压纠偏装置的整体结构设计,提高其模块化和标准化程度,方便维护和升级。采用更加轻量化和高强度的材料,减轻装置重量,提升其工作效率和耐久性。
开展多学科交叉研究:液压纠偏装置的性能优化不仅涉及机械工程和液压技术,还涉及电子控制、材料科学、计算机技术等多个领域。通过多学科交叉研究,集成各领域的最新成果,推动液压纠偏技术的不断创新和发展。
液压纠偏装置性能优化是一项复杂而系统的工程,需要从硬件到软件,从理论到实践,多方面协同推进。通过不断探索和创新,液压纠偏装置将会在未来的工程机械领域发挥更加重要的作用,助力企业在激烈的市场竞争中取得更大的优势。